What We Do
MingHe is a metal products company that manufactures components for the world's most demanding applications. With our unmatched diverse capabilities and depth of experience, we are relentless about working with our customers through their entire journey – from product design to delivery.
Work Materials
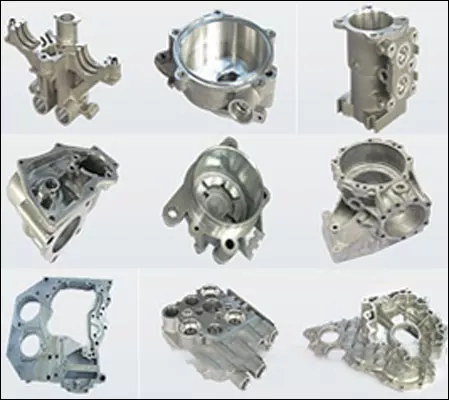
Aluminum Casting
Minghe is an expert in aluminum die casting. Aluminum has excellent corrosion resistance, mechanical properties, and high thermal and electrical conductivity, making it an ideal alloy for die casting.
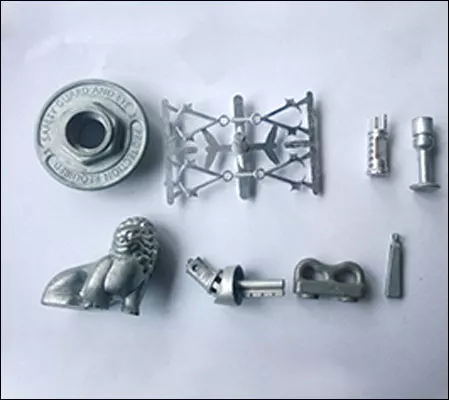
Zinc Casting
Zinc is a low-cost raw material. Minghe is a world-leading precision zinc die caster. We have produced billions of zinc die-castings, with sizes ranging from a fraction of a gram to one kilogram.
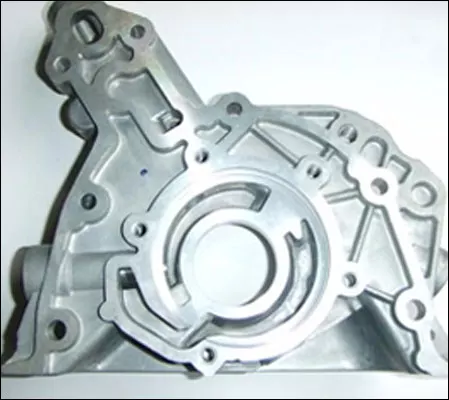
Magnesium Casting
We have extensive experience in magnesium casting, including magnesium die casting. We have strong capabilities in casting various magnesium alloys such as AZ91D, AM60B, and AM50.
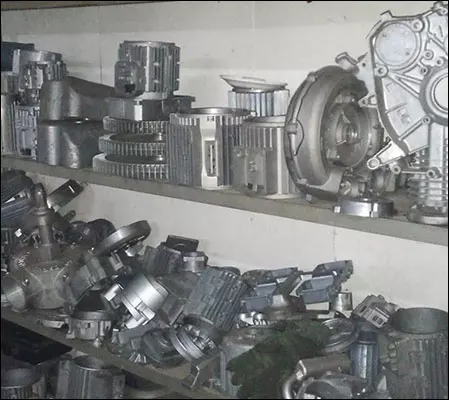
Other Casting Materials
Bringing design to life. For 35 years, Minghe has been dedicated to providing high-quality die casting, molds, parts, and comprehensive services to companies through advanced machinery and processes.